Illinois Thermal Imaging Services
» Electrical Preventative Maintenance
By far, the most popular and widely used application of infrared thermography is electrical components testing. The widespread popularity among building owners is due to the fact that studies have shown that for every $1 spent on electrical preventative maintenance there is at least a $4 return on their investment because of the savings in downtime and premature equipment replacement. EPM is an invaluable tool in any P/PM, because it saves money!!
How It Works
Infrared thermography is used to perform P/PM inspections on electrical equipment because excess resistance on electrical apparatus indicates electrical faults such as loose connections, overloaded or imbalanced circuits, faulty breakers, damaged switches, faulty fuses and a wide range of other unwanted electrical conditions. Before an electrical component burns up, it heats up. Thermography is used to see the excess heat (resistance) so that problems can be found and maintenance personnel can act to correct the problem before the component fails, causing damage to the component, safety hazards and/or production downtime.
Advantages of an Electrical Maintenance Scan
- Reduce Downtime
- Increase Equipment Life
- Lower Risks
- Comply with Electric Codes
- Lower Repair Costs
- Increase profits
- Save on Insurance
- Prevent Catastrophic Failures
- Save Lives!
What Electrical Distribution Equipment Should Be Checked?
- Utility substations, transformers and feed poles
- Main incoming services, plant main knives
- Capacitor banks
- Main switchboards and disconnects
- Main distribution panels and main disconnects
- Uninterruptible power supplies
- Generator controls and transfer switches
- Main I-Line panels
- Lighting and receptacle panels
- Disconnects and combination starters
- Service disconnects for motors
- Machine control panels
The National Fire Protection Agency (NFPA) and the International Electrical Testing Agency (NETA) prominently recommend the use of infrared inspection in the testing and maintenance of electrical systems and components.
National Fire Protection Agency: NFPA 70B
Recommended Practice for Electrical Equipment Maintenance, 2002 edition
“Infrared inspections have uncovered a multitude of potentially dangerous situations. Proper diagnosis and remedial action of these situations have helped to prevent numerous major losses”-20.17.1.1
“Routine infrared inspections of energized electrical systems should be performed annually prior to shut down. More frequent infrared inspections, for example, quarterly or semiannually, should be performed where warranted by loss experience, installation of new equipment, or changes in environment, operational, or load conditions. 20.17.5
“Infrared inspections of electrical systems are beneficial to reduce the number of costly and catastrophic equipment failures and unplanned plant shutdowns” 20.17.1
“Many organizations are finding that it is preferable to obtain these surveys from qualified outside contractors. Because of their more extensive experience, their findings and recommendations are more likely to be accurate, practical and economical then those of a part time in house team” 20.17.3
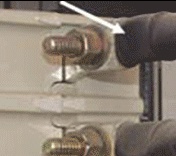
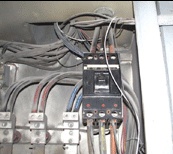
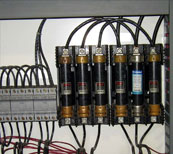
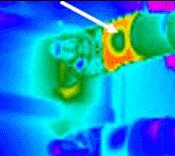
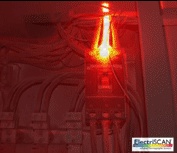
» Contact Us
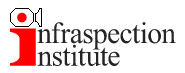
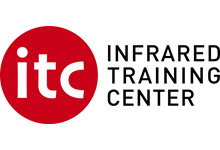
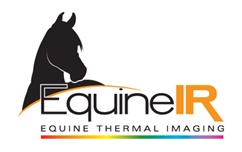
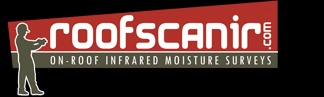
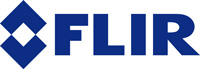